Inside the Steinway piano factory in New York
Since its founding in 1853 in a manhattan loft on Varick street, Steinway & Sons has been considered the one of the world’s finest piano manufacturers. Over the next thirty years, German immigrant Henry Engelhard Steinway and his sons developed the modern piano, building each instrument one at a time. now — more than 160 years later — the grands, uprights, limited-editions and special collections are still primarily constructed by hand, using skills passed down from master to apprentice over several generations.
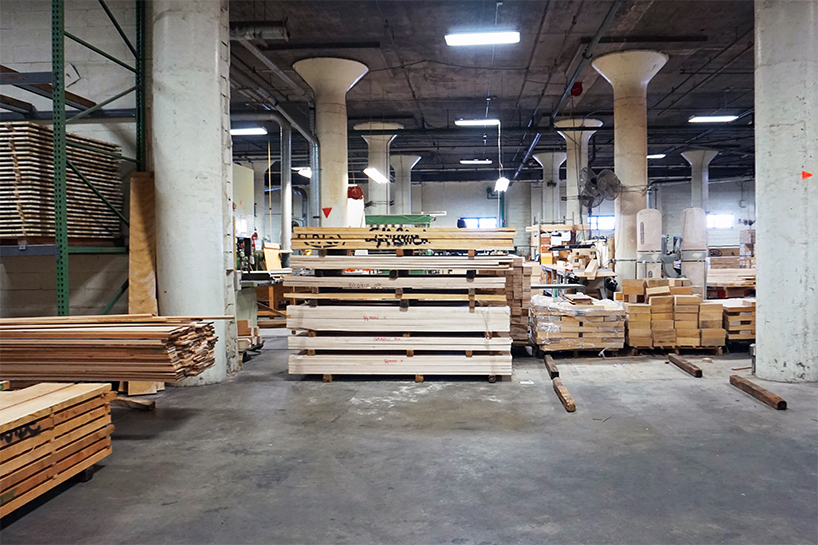
85% of every piano is wood, which starts as lumber, air dried for up to one year
Every single Steinway is crafted by a team of dedicated artisans with decades of experience, who take pride in humanizing each object using many of the processes which have remained essentially unchanged since the brand’s early years. built in one of two company-owned and operated factories — Astoria, New York and Hamburg, Germany — with more than 12,000 individual parts, every instrument bears its own musical character and is as distinctly unique as the pianist who plays it.
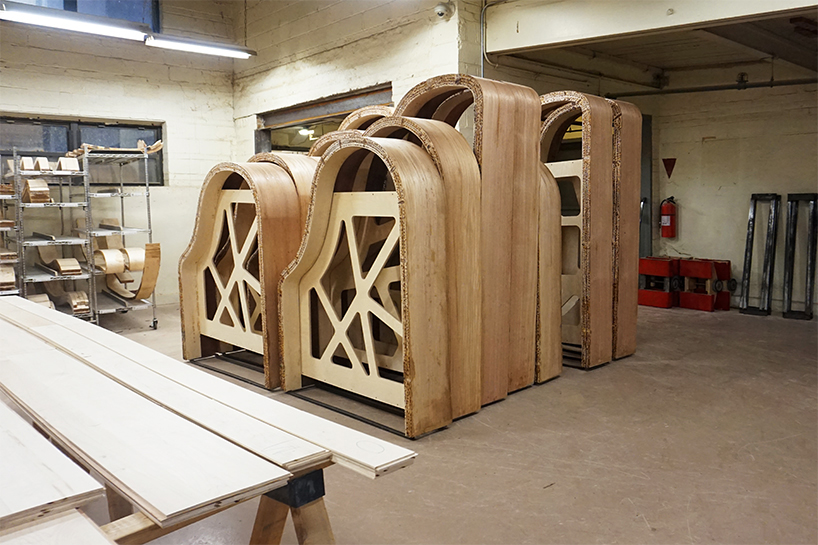
Maple wood is laminated and glued together in sets to produce piano rims (finished, above)
To document the making of a piano, Designboom went inside the Steinway factory in New York. Every aspect of the instrument’s evolution from a stack of wood to a playable piece has been expertly considered and carefully executed. laborious procedures are carried out alongside meticulous ones: the rim-bending process sees a series of craftsmen carry laminated wood onto large metal presses, which they then forcefully clamp into place to create the piano rim; an Italian artisan working at Steinway for more than 30 years carefully hand carves ornamental details for special editions like the Louis XV and the Chippendale. see Designboom’s walkthrough of the factory’s workshops, restoration rooms, and storage spaces to see the craftsmen at work, below.
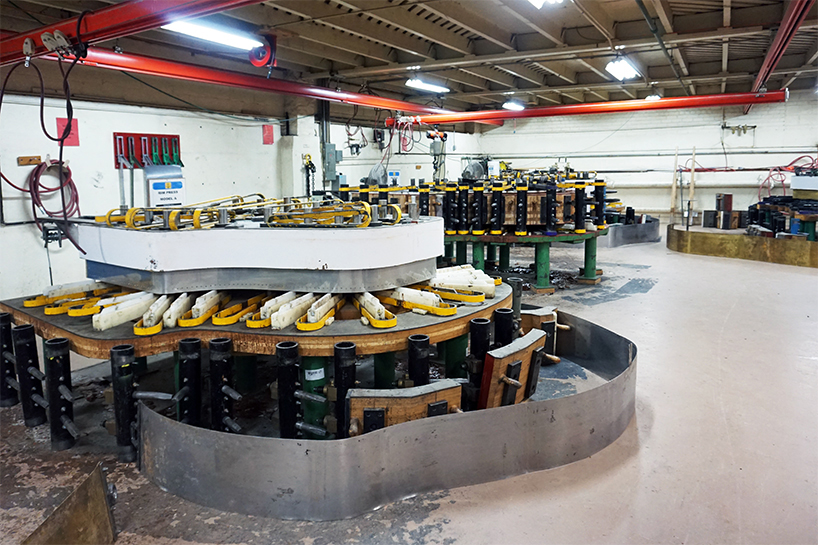
Each model piano is represented in this room filled with presses, which shape the laminated wood into the rim
Additionally, the company recently revealed the ‘Steinway Spirio’, a player piano system which performs at the same standard as a concert pianist. in conjunction, a new initiative sees three creatives over a period of three years use this instrument as an artistic medium, finally pairing the reinterpreted piano with a Steinway musician, who composes a score specifically for that piece. see the first realized work in the series by LA-based artist mark Bradford on Designboom, here.
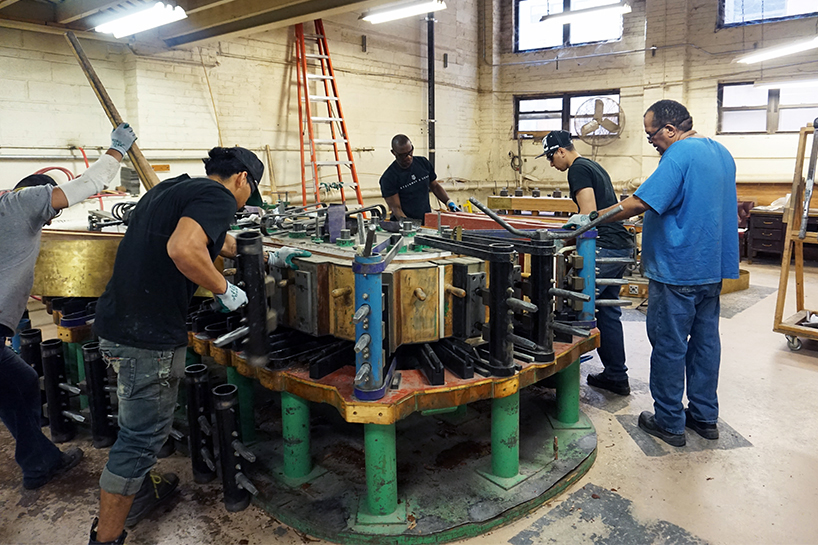
The sets of maple are carried to the press and clamped into position
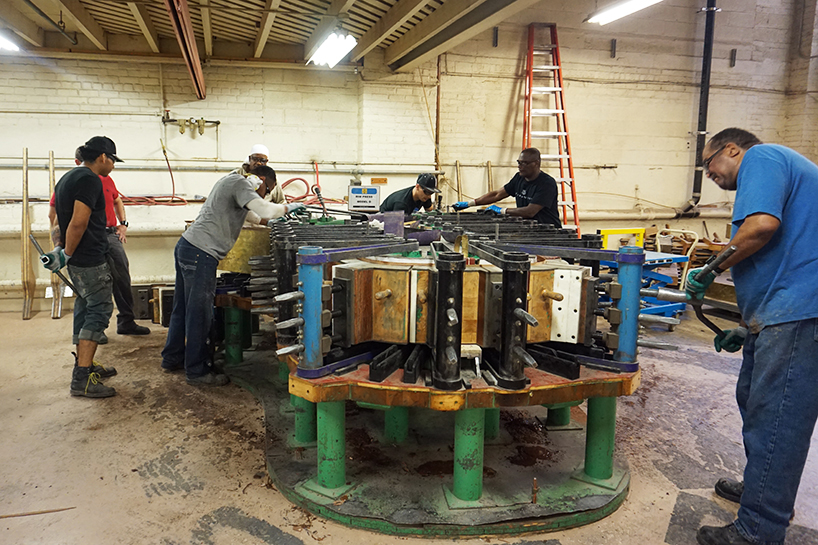
Craftsman work from the center outwards, tightening each of the clamps into place
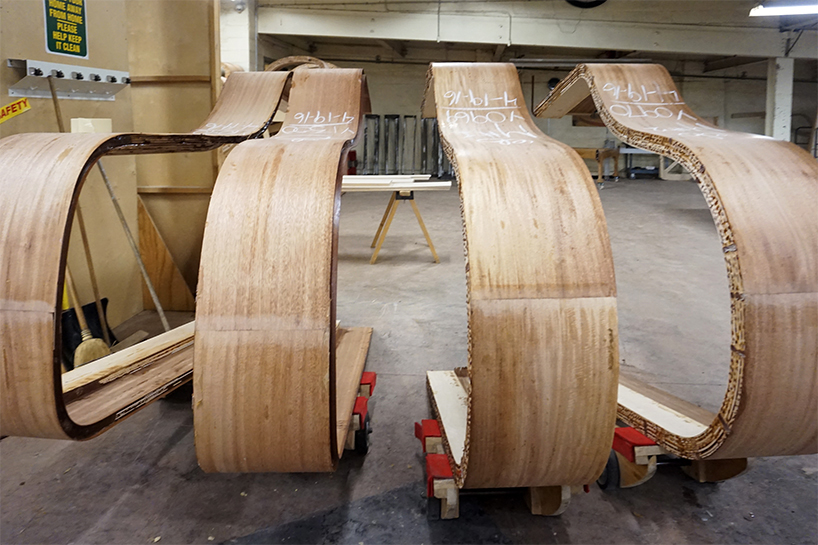
After 24 hours, the rims completed the previous day are removed from the press
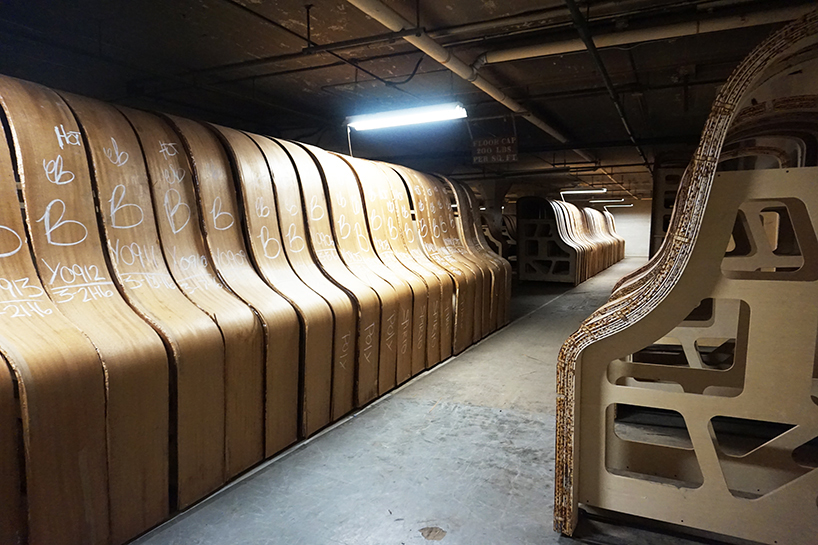
The finished rims are transferred to this conditioning room, where they are stored for several months
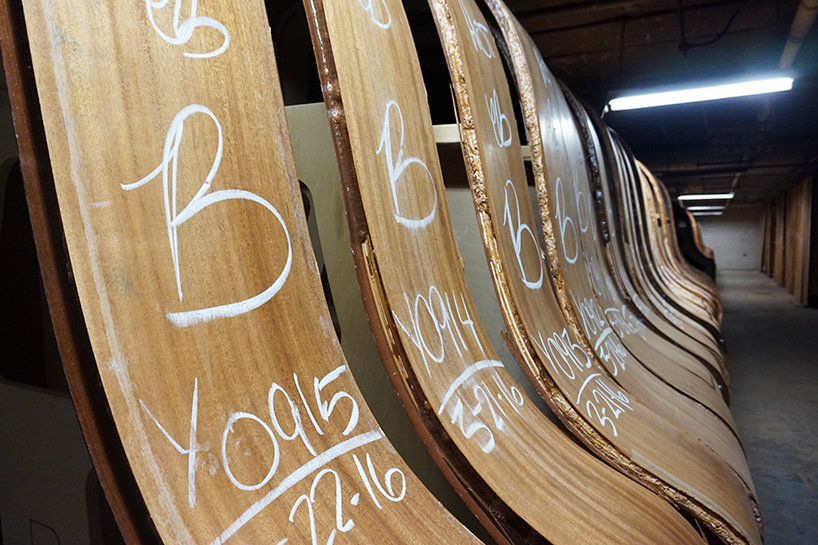
Each piano is marked with a unique number that it maintains throughout the production process
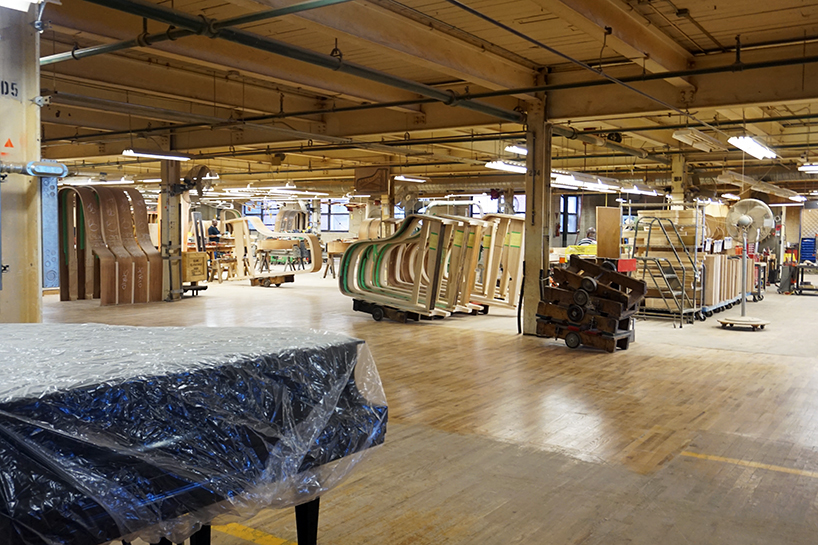
Piano rims are prepared in the factory for their following stages of production
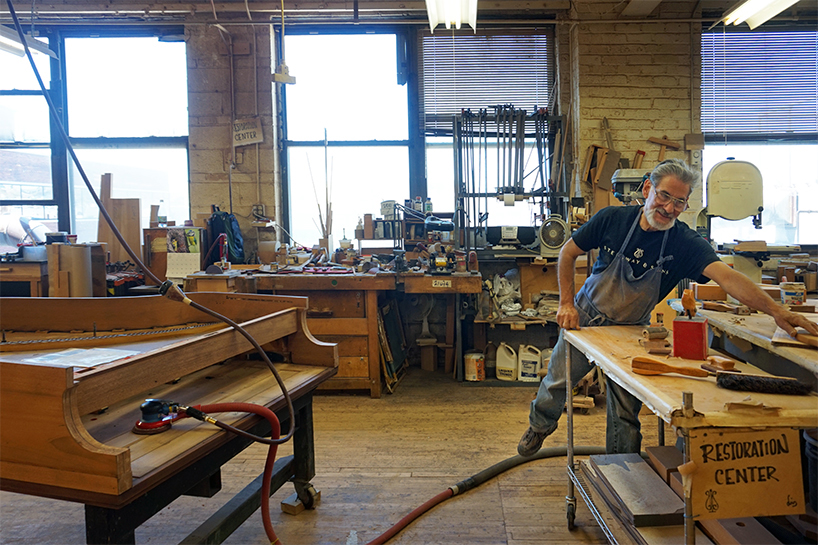
An onsite ‘restoration center’ is where artisans work to repair older models for modern use
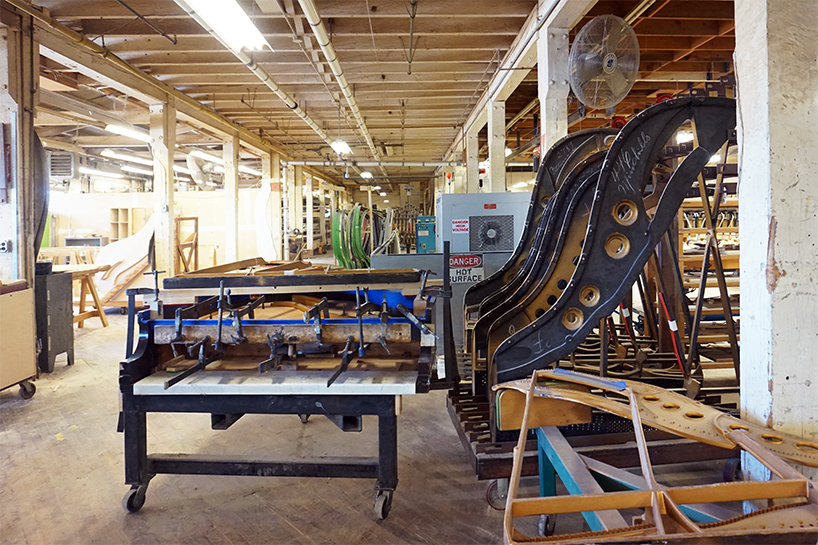
Iron plates from older pianos are painstakingly restored
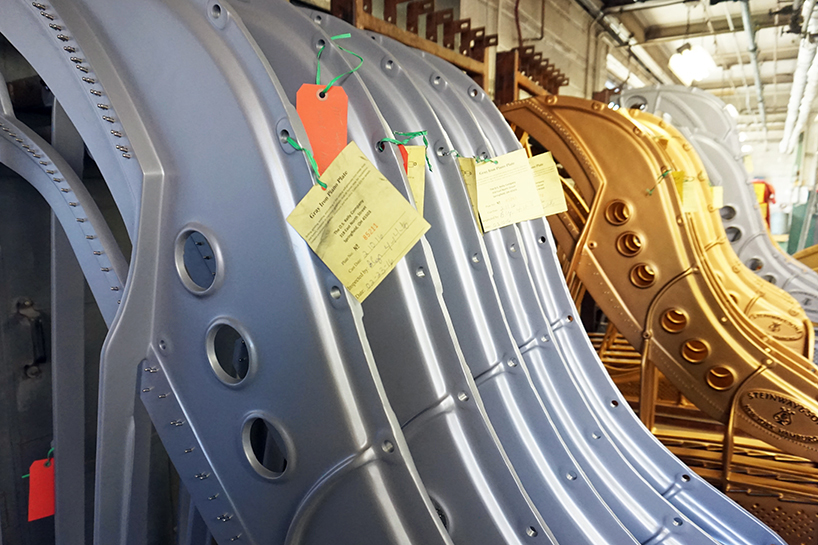
New iron plates are organized before being assembled into place

A craftsman chips away at parts of the bridge, made of vertical laminated maple
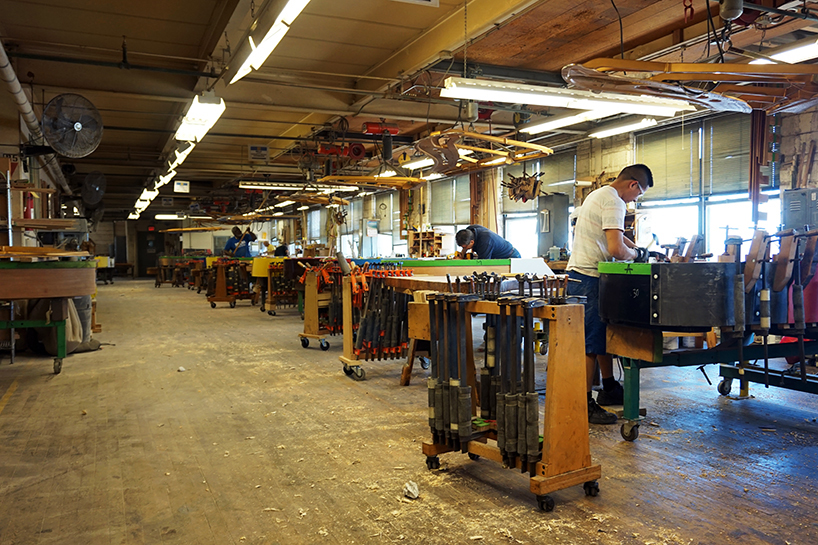
Artisans work on soundboards and bridges, with iron plates ready to be fitted suspended above them
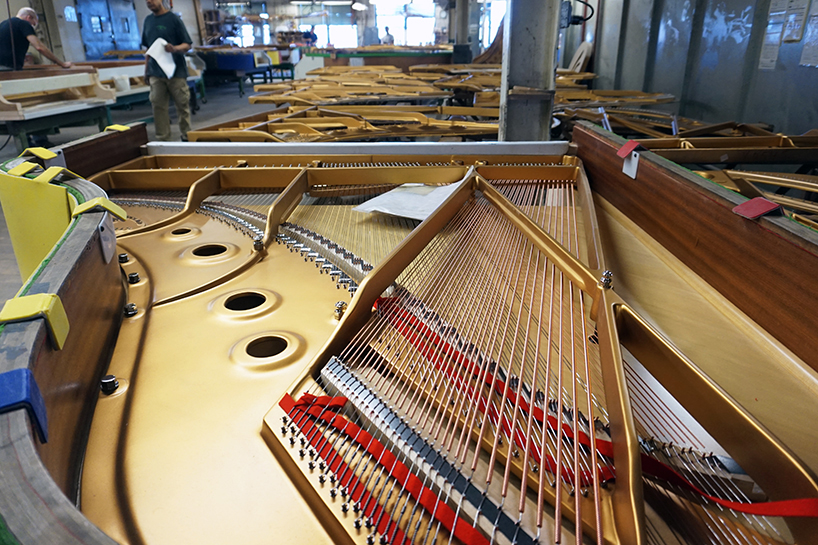
After the iron plates have been assembled, strings are attached through a mix of hand and machine-made processes
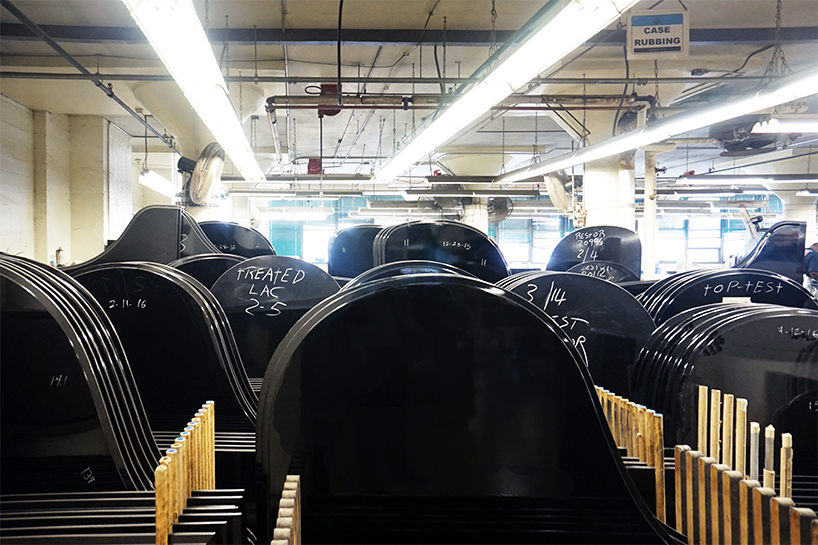
Black-painted piano tops are organized according to model and size
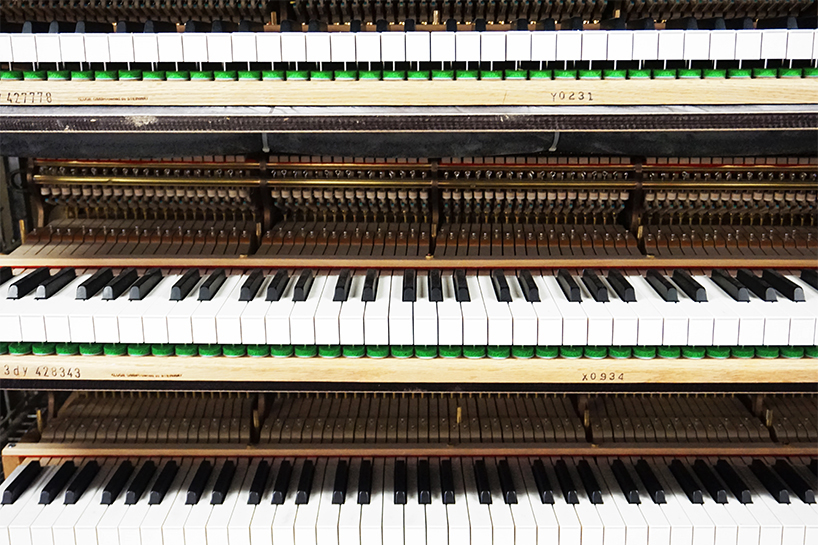
A stack of key frames wait to be fitted into their respective pianos